Lithium-ion Battery Recycling Ecosystem: Key To India's Green Goal?
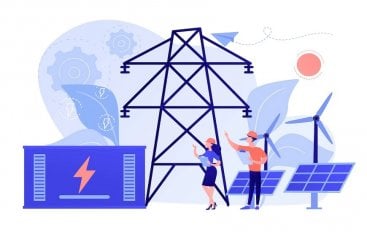
The tech-savvy modern consumer regularly switches to the latest gadgets and solutions. While this trend fares well for many global manufacturers, it also leaves a large pile of e-waste behind. According to the Global E-waste Monitor Report, nearly 53.6 million metric tons (MT) of e-waste were generated in 2019. This number is expected to balloon to 74.7 million MT by 2030.
E-waste is a global problem that is driven by the technological advancements taking place in various industries across the world. There must be a proper plan for managing the e-waste emanating from various corners of society in the country. With India pushing the pedal on adopting electric vehicles in a big way in the future, it is expected that the e-waste volume from EVs will grow exponentially in the coming years.
Close to 30 per cent of private and 70 per cent of commercial vehicles will likely be converted to EVs by 2030 in the country. The share of Li-ion battery recycling will likely increase exponentially in the coming years.
Challenges in e-waste and Li-ion batteries recycling
In addition to the EVs, Li-ion batteries are used in various consumer durables, electronics, energy storage devices and the telecom sector. While EV batteries e-waste is either the one recalled by manufacturers or from the manufacturing waste, the other segments attract majorly end-of-life li-ion batteries to the recycling ecosystem.
Here are some of the challenges that need to be handled:
Informal sector
India is the third-largest e-waste generator globally, after China and US. While e-waste is not harmful if collected, stored, and recycled correctly, only 10 per cent of e-waste generated in India is appropriately collected and recycled. There is a need to have outcome-based regulation to help better implement the Li-ion batteries recycling and recycling e-waste in general.
There is a need to deploy world-class technology for maximum extraction of valuable metals from li-ion batteries. Unlike the case with e-waste, where the informal recyclers can recover metals like gold and silver, although using an unscientific approach, it is not possible in the case of Li-ion battery recycling. It is mainly because the process knowledge for li-ion battery recycling has not been passed from one generation to another, unlike e-waste recycling.
Tracking of e-waste
E-waste tracking is critical to ensuring that the policy framework can deliver the expected results. There are challenges in tracking e-waste from the cradle to the grave and cradle to cradle. It needs to be resolved to ensure natural circularity in the industry. An effective e-waste tracking mechanism can help check the li-ion e-waste disposal system and develop sustainable linkages among stakeholders. It will also improve the overall adoption of the e-waste ecosystem. The government has introduced the concept of extended producer responsibility (EPR). Under this, the producer must ensure that the end-of-life products get collected and recycled.
Investment in R&D would ensure that more Li-ion e-waste is recycled in India than exported. However, the most prominent e-waste industry players are traders who do not invest in R&D or technological advancements. As a result, most e-waste from India is exported with no economic or social benefit to the country.
The solution to the rising e-waste challenge
The challenges emanating from technological advancements can be resolved by technology itself. With all the industry's challenges, multiple solutions can be implemented for better efficiency and results. For instance, a software system can be deployed to track materials from cradle to cradle in the Li-ion battery ecosystem and other materials that generate e-waste. It would help establish a circular economy and enough safeguards to ensure that the regulations are followed and implemented correctly.
Recyclers operating in the country can connect to a central system for better tracking and efficiency. This can emerge as a system where more efficient recyclers can get production-linked incentives based on their output. It will help track the progress and the contribution of each entity's inefficient recycling.
Around $100 billion have been invested globally in the Li-ion battery ecosystem from a manufacturing standpoint; regulations need to ensure a minimum investment from each recycler into R&D and zero emissions and environmental safety. The assets in R&D will result in better industry practices. At the same time, this will lay a strong foundation for the long-term e-waste plans of the country.
Another essential intervention can be disincentivizing exports of e-waste. By exporting most of the e-waste, the country cannot create an image of a proactive environment saviour in the global community. It will also create a win-win situation for the country and the industry in the long run. The government can take the lead here to ensure that e-waste recycling is established as a practice rather than opting for a short-term solution of exporting e-waste.
There is a need to ensure a circular economy in the Li-ion battery recycling ecosystem. Through regulations, incentives or awareness campaigns, establishing a circular economy in the Li-ion battery recycling framework will help efficiently use raw materials and put less burden on the environment.
Role of PLI Scheme
The Government of India's production-linked incentive (PLI) scheme is impactful in driving the manufacturing landscape in the electric vehicles industry. An increasing number of manufacturers are expected to take advantage of the incentives available in the scheme and increase their exposure to the manufacturing of electric vehicles.
However, it does not cover materials that are essential in ensuring the sustainability of EVs and renewable energy in India. By covering materials, the regulations would also make way for the recycling of Li-ion batteries, which is essential to ensure sustained growth of electric vehicles in the country.
Road ahead
There is no doubt that exciting times are ahead for several industries that are pushing frontiers in technological advancements, including electric vehicles. However, there needs to be enough focus to ensure that e-waste recycling is handled correctly. To start with, more significant support for scientific recycling and tracking of materials from cradle to cradle to ensure circularity is the need of the hour.
The roadmap ahead can be divided into short-term and long-term measures required. For instance, quick measures like providing recycling licenses to organizations with the right technology and equipment, removing dismantlers from the list, and allowing CPCBs to take the lead role in this exercise rather than relying on SPCBs would reduce red tape and increase efficiency.
At the same time, long-term benefits like extending the PLI scheme benefits to recyclers who produce end metals and materials rather than OEMs using recycled materials can be taken. These solutions can provide the right footing for handling the increasing e-waste efficiently.
(The above-given article is attributed to Nitin Gupta, Co- founder and CEO, Attero Recycling)