Significance of Supply Chain Resilience for now and the future
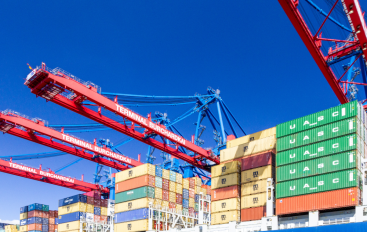
Natural disasters are commonplace in India. Every year, India faces disruption due to disasters such as floods, earthquakes or landslides. According to the Global Climate Risk Index report 2019, India is the 14th most vulnerable country in the world. But over the last year, Indian enterprises have had to prepare for a completely different kind of disruption brought upon by Covid- 19. Consequently, this disruption caused huge supply chain challenges for every organization.
Every disaster exposes an organization to several supply chain vulnerabilities. In an August 2020 report titled, ‘Risk, Resilience and Rebalancing in global value chains’, McKinsey pointed out that companies can now expect supply chain disruptions lasting a month or longer to occur every 3.7 years. In an increasingly connected world, enterprises must seek to be more resilient to supply chain shocks, as it can threaten their competitiveness and survival.
Supply chain resilience can no longer be ignored
The supply chain has always been traditionally viewed as a cost center. Today, the reality is far removed from this way of thinking. Supply chains are critical to operations, efficiency, and long-term success of the business. The devastating effect of Covid-19 pandemic has exposed several structural vulnerabilities within supply chains that can no longer be ignored. In 2020, according to the Supply Chain Resilience Report 2020, the Covid-19 pandemic was the biggest threat to global supply chains. This was much more than supply chain shocks that have occurred due to trade sanctions, natural disasters, and cyberattacks combined. In all, around 60% of those surveyed said that the pandemic had directly disrupted their manufacturing supply chains. As a result, 96% of companies are planning to build resilience into their supply chain.
Key components of supply chain resilience
At a high level, a supply chain resilience model combines both resistance and recovery components. The combination you select is likely to be driven by your organization’s specific supply chain needs and available budget. Resistance is the supply chain’s ability to minimize impact of disruption – such as a natural disaster by either evading it entirely or by minimizing the time between beginning and end of the effect of disruption on supply chain. Recovery is the supply chain’s ability to return to full operations once a disruption has occurred.
From ‘just in time’ to ‘just in case’
Companies have had concerns about the structure, robustness, and resilience of global supply chains. Now, they are looking to manage risk by striking a different balance between just-in-time and just-in-case – building supply chains that are flexible and responsive with sufficient padding to absorb the worst effects of a shock. This requires robust digital platforms that let trading partners communicate and collaborate effectively, as well as the analytics muscle to run scenarios based on different responses to potential disruption.
There are a number of supply chain resilience strategies that organizations can follow to achieve a just in case strategy. These include:
Inventory buffers: Buffer capacity is the most straightforward way to enhance resilience, whether in the form of underutilized production facilities or inventory in excess of safety stock requirements. However, this approach is expensive. A company must pay for the redundant stock, capacity and workers. In addition, it goes against lean principles that supply chains have been following for years that could lead to a drop-in efficiency and quality
Multi-sourcing: Multi-sourcing is a good way to mitigate this risk by building a supplier network that enables the organization to quickly select an alternative supplier to deal with disruption and ensure business continuity. There needs to be end-to-end transparency and visibility across your global supply chain, extending beyond tier-one suppliers to cover their vendors and their vendors’ suppliers
Nearshoring: Covid-19 has seen national governments and organizations worry about the safety of supply of essential products. As a result, many companies are now exploring the ability to reduce geographic dependence in their global networks and shorten cycle times for finished products by bringing production back to domestic markets. Regional or local supply chains can be more expensive, but they allow for more control over inventory and move the product closer to the customer
Ecosystem partnerships: The Covid-19 crisis has shown the need to have a diversified approach to sourcing. At the same time, collaboration with partners such as strategic raw material suppliers and external service partners is vital to ensure better preparedness and resilience.
The Covid-19 crisis has helped in raising the bar for improving supply chain resilience. In a Gartner survey last year, only 21% of respondents stated that they have a highly resilient network. More than half expected to be highly resilient within two to three years. Given this context, it’s more important than ever that organizations take proactive steps to build resilience in their supply chains. While no strategy is foolproof, those organizations that can effectively manage risk will not only build supply chain strength and agility, but they will also succeed in significantly increasing their competitive advantage.